"Laser welding machines are now industrial and reliable".
Emric Verwaerde, Managing Director of Laser Cheval, explains laser technology in detail. A high-precision technology where innovations are constant. However, it has not yet conquered all the industrial sectors for which it offers high performance, thanks in particular to laser welding.
Can you explain how laser welding works?
Emric VERWAERDE: Laser welding is based on the use of light to heat and melt the area to be welded, known as "the joint". This light comes from a laser, an acronym for Light Amplification by Stimulated Emission of Radiation. In other words, the laser converts energy into light, which is then optically amplified. This light, whose wavelength (or color) depends on the material used to generate it, can range from ultraviolet to infrared.
Laser Cheval uses near-infrared sources (+/-1060nm). This wavelength enables high power levels to be achieved, and is suitable for most metals, including those with high reflectivity (such as gold or aluminum), thanks to its high power density.
What are the advantages and limitations of laser welding compared with arc techniques (in terms of materials, performance, weld quality, etc.)?
Emric VERWAERDE: The laser is not a true competitor to traditional processes, but rather a complement, with several advantages:
- High precision: The laser beam can be focused on a very small area (D.25µm), enabling high-precision welding even in hard-to-reach areas.
- Speed: Laser welding is extremely fast, especially when combined with scanners, making it highly effective for industrial applications with speeds ranging from 20 to 100 mm/s.
- Less distortion: Thanks to the high speed and short interaction time between the laser and the material, the heat-affected zone is reduced, thus minimizing distortion of the parts.
- Weld quality: Laser welds are generally of higher quality, and require little post-treatment. The process can even produce invisible welds when aesthetics are an important criterion.
- Automation: Laser welding is easily automated, making it perfect for mass production.
How long have lasers been used for welding, and when were the first industrial solutions developed? Which industries use this technique today?
Emric VERWAERDE: Laser welding is a relatively recent technology, with industrial applications dating back over 50 years. Laser Cheval sold its first welding machine in the 1980s, mainly for the jewelry industry, and during the same decade, the technology developed further, notably in telecoms and electronics, in addition to the luxury goods sector.
Today, laser welding is used in a wide range of industries. At Laser Cheval, we manufacture around 10 laser welding machines a year for the luxury goods, medical, electronics and other sectors.
What are the different types of lasers used for welding, and what are their advantages and disadvantages?
Emric VERWAERDE: As far as the equipment is concerned, the main component is the laser source, chosen according to the wavelength needed to optimize absorption of the materials to be welded, but also according to its cost. For example, if one wavelength is twice as effective but five times more expensive to produce or operate, it's better to opt for the former and increase the power.
This is one of the reasons why Laser Cheval focuses on the near infrared, as this wavelength is economical and easy to produce.
The laser beam is then transported by optical fiber, simplifying integration and maintenance. In terms of machine structure, there are two main types: those where the workpiece moves relative to the laser, and scanner machines where the laser moves over the workpiece using 2 mirrors mounted on galvanometric motors.
Given that laser welding is less widespread than other welding techniques, how do you train welders in this technology?
Emric VERWAERDE: Training in laser welding is relatively rare in France, but the basic principles are the same as for other welding techniques, since the laws of physics are identical. We therefore recruit technicians with a background in mechanics and metallurgy. If these technicians have no experience of laser welding, we can provide them with in-house training. Every year, we train around fifty customers in the use of our laser machines.
What areas of research and development have you focused on in recent years? Can you tell us about your latest innovations and the evolution of your laser welding offering?
Emric VERWAERDE: In recent years, we have focused our development efforts on two main areas:
- Technical: We have been working on a number of innovations, in particular to achieve micro-welding with specific constraints, such as "invisible soldering on gold parts", "tight soldering of thin membranes", or "soldering of small wires on contacts". This research involved equipment testing (types of sources, fibers, gas protection, etc.) as well as process development (paths, temperature control, positioning, etc.).
- Machine control: At the same time, we perfected software tools to make the technology even more accessible. This includes tools to facilitate machine parameterization and process automation, with, for example, the introduction of video assistance.
How do you see the laser welding market evolving in the coming years (automation/robotization, new applications and interested industries...)? Are there still any obstacles to deployment?
Emric VERWAERDE: The main obstacle to the development of laser welding remains the lack of knowledge of this technology in design offices. As with all technologies, laser welding is only really effective if the design of the parts is adapted to this method. All too often, it is used as a last resort, once other techniques have failed.
Today, however, laser welding offers many advantages and should be considered right from the design phase, just like other assembly processes. Laser welding machines are now industrialized and reliable, and their use will continue to simplify. Costs have fallen and continue to fall. More and more players, like Laser Cheval, are able to develop laser welding machines and processes. As a result, the market will continue to grow.
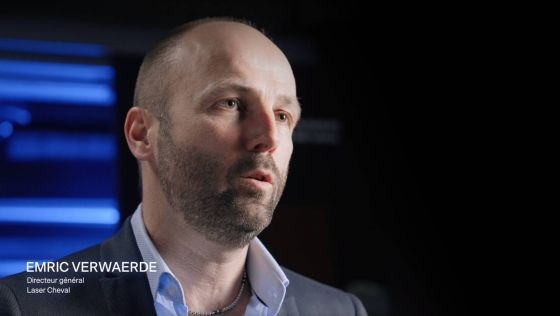